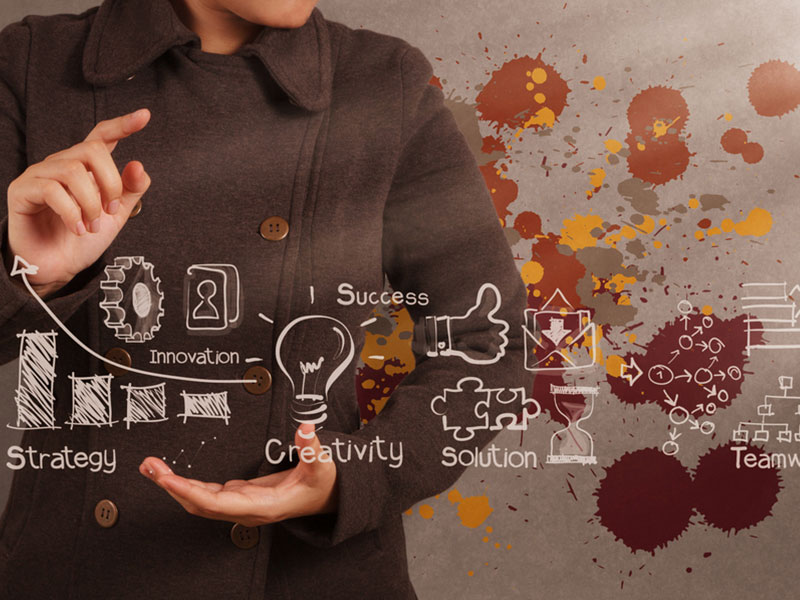
Lean Thinking and Six Sigma: Two Different Yet Complementary Thinking Models
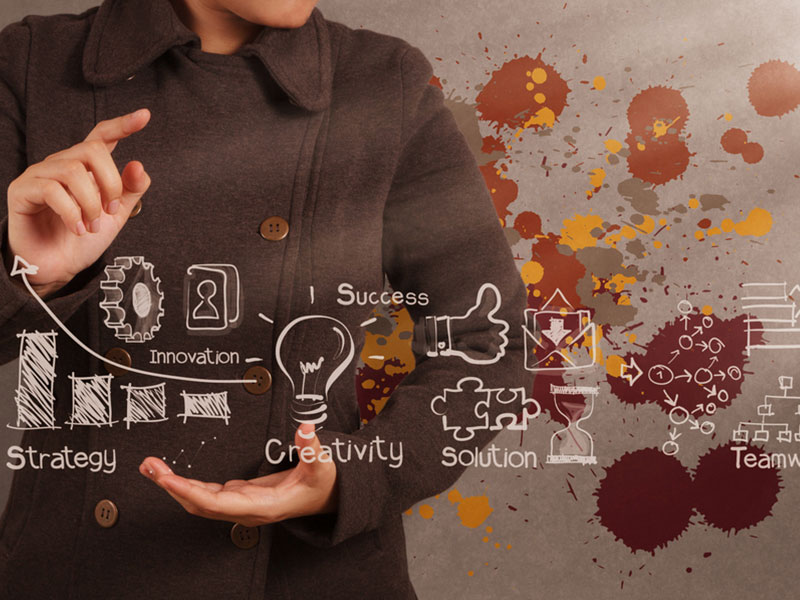
Training you brain helps you think better. One way of training you brain is through thinking models. In short, a thinking model is an explanation of how something works. It is a series of steps, or a concept, that you carry out in your mind to help you see and understand the world and the relationship of things. Through these steps, you can generate ideas and come up with innovative solutions. In this post, I will be talking about two well-known thinking models: Lean Thinking and Six Sigma.
Lean Thinking
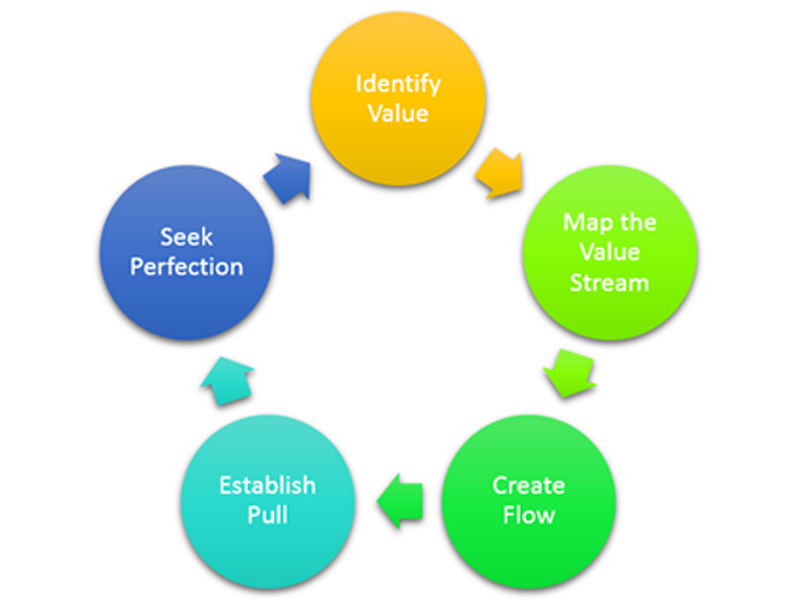
The term Lean Thinking was first used by James P. Womack and Daniel T. Jones to describe the scope of their intensive studies they conducted on the Toyota Production System. The Lead Thinking model is a mindset, rather than a procedure. It is focus oriented, putting the customer needs and return on investment first, whilst eliminating anything which is valued as a cost. Its aim is to create a lean workflow within a company, sustaining growth by aligning customer and employee satisfaction, which in return will minimise costs.
In a nutshell, the Lean Thinking model works by following these steps:
- Identifying activities that create or add value;
- Determine the sequence of activities;
- Eliminate activities that do not add value;
- Allow the customer to “pull” products and services;
- Improve the overall process.
This method is seen in small companies and internet businesses. As they do not have any buffers, such as data inputting, order placement etc., in between order-to-delivery (in the case of design, it can be concept-to-prepress), it maximises efficiency and minimises costs. It makes up for a lean workflow.
The Lean Thinking model also utilises the 5S System of Organisation. This system tackles the environmental aspect of the workplaces. Essentials, according to this system, a messy workplace makes it difficult to find things, get distracted more easily and may also be hazardous. The 5S’s stand for:
- Sort – sort out what is needed the most
- Set in Order – put things in their suitable place
- Shine – clean up the workspace
- Standardise – Set a standard for the firt 3S’s
- Sustain – Make the 5’s the norm
The Lean Think model is very visual; it relies on observation. It focuses on workflow and processes. Some perceive it as radical, for it is a ‘people first’ model, plus it focused on individual customers that than the whole market. In addition, it also teaches employees on how to learn, rather than showing the employees what should they do. This is because through Lean Thinking, an employee is expected to develop a sense of autonomy.
Nowadays, Lean Thinking is also being extended to help companies reduce their carbon footprint. Just like waste can be eliminated by reduces processes, it can also be applied to reduce actual waste by printing less, using washable cups and being mindful when using electricity and water.
Six Sigma
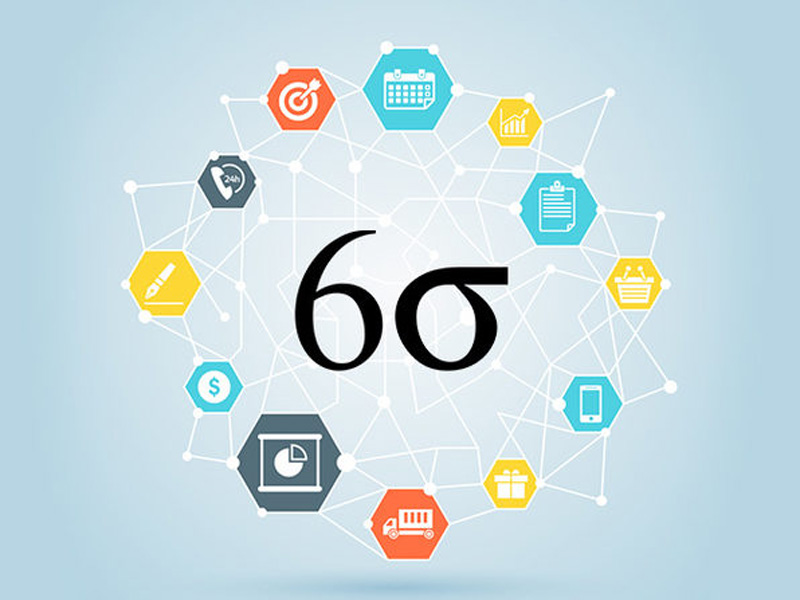
Six Sigma is a problem focused thinking model. This model utilises statistics to understand variation, unlike Lean Thinking, which relies on visualisation of a situation. Six Sigma was introduced by Bill Smith, an American Engineer who worked at Motorola in 1980. Later it was also used by Jack Welch for his business strategy at General Electric in 1995. This thinking model is one in where 99% of all chances to create something, it is statistically proven that it will be defect free. The term Six Sigma was trademarked by Motorola in 1993.
As a thinking process, Six Sigma seeks to improve the overall quality of the output of a process, service or end product by pinpointing and eliminating the causes of defects whilst keeping variability in production to a minimum. For maximum efficacy, Six Sigma uses two different methodologies:
- The DMAIC:
- Define
- Measure
- Analyse
- Improve
- Control
- The DMADV (also known as DFSS – Design For Six Sigma)
- Define
- Measure
- Analyse
- Design
- Verify
These methodologies are used individually depending on the case in question. However, within both methodologies, Six Sigma still uses many other popular tools which are also known and used outside the Six Sigma thinking method. These include the 5 Ws, Histograms, Statistical tools (Correlation, Scatter Diagrams…) and cost-benefit analysis.
The DMAIC model is more popular. It is often used by scientists, as they collect data, analyse it and take note of all statistics and zero in on the problem. After that they will look at their findings until they can make links, test out possible solution and come up with a solution. Similarly, the DMADV model is used by designers and often the end product is something tangible. Also, the DMADV may use slightly different tools in the process, being a methodology that is applied in a different industry. In spite of that in both cases, there is a testing phase to ensure that the final solution is truly the ultimate one.
Over the years, Six Sigma has proven that is one of the most efficient thinking models, that has benefitted the business strategy for multiple Fortune 500 companies. These include engineering, finance, manufacturing and healthcare. Despite this, some experts argue that Six Sigma is overrated. Joseph M. Juran referred to Six Sigma as “a basic variation of quality improvement”, stating that there was nothing new. Similarly, quality expert, Philip B. Crosby highlighted that the Six Sigma method does not go far enough, meaning that customer deserve product free from defects every time. Some other point out that this thinking method relies too much on numbers and graphs. According to John Dodge, Six Sigma is not appropriate for research environments as it inhibits creativity, due to the overwhelming volume of statistical data.
In Comparison
Although different, these two models are quite similar. Firstly, both thinking models make a clear statement that waste should be eliminated. Through Lean Thinking, one can get rid of all the evident waste, whilst Six Sigma allows sifting to find even minor problems that may be causing major setbacks. Moreover, Lean Thinking is more suitable for smaller businesses, whereas Six Sigma is better for larger companies. Lean Thinking is a good springboard for business who would like to improve the workflow and their turnaround time. Six Sigma on the other hand can take longer to implement as it has a longer analysis phase. Having said that, it should not be the case of ‘one or the other’ but rather a case of a coupling of an even bigger thinking system, taking the best parts from each thinking model according to each situation. That way, it can pave the way towards the ultimate thinking model.